www.endustriweb.com
18
'17
Written on Modified on
Üretimde Iskartayı Kontrol Etmeye Yönelik Pratik Bir Yaklaşım
Üreticiler sürekli olarak üretkenliği ve verimliliği en üst düzeye çıkarmanın yollarını arar. Bugün, bu çabalar sıklıkla bulut bilişim, veriye dayalı üretim, siber fiziksel sistemler ve Industry4.0 gibi moda sözcükler içeren yüksek düzeyli programlar içermektedir. Bu ileri düzey girişimler harika konseptler ve etkileyici sonuçlar sunabilir. Ancak, üretim gerçekleri genellikle bu tür iddialı planların uygulanmasına müdahale eder. Kritik bir gerçek de üretim sürecinde kaynakların iyi kullanılmamasından oluşan ıskartaların kontrol edilmemesidir. Bir üreticinin dijitalleşme ve iyileştirmeyi tartışmadan önce, operasyonlarını incelemesi, kaynakların nerede iyi kullanılmadığını belirlemesi ve bunu azaltacak veya ortadan kaldıracak yöntemleri geliştirmesi gerekir. Bir üretim şirketini gelişmiş, akıllı üretim stratejilerini benimsemeye hazırlayan ilk adım iyi kullanılmayan kaynakların kontrol edilmesidir. Şekil 1 – Tüm unsurların ve bir üretim tesisinde bunların birbirleriyle nasıl ilişki ve etkileşim içinde olduklarının toplam resmi (NEXT STEP modeli ve konsepti).
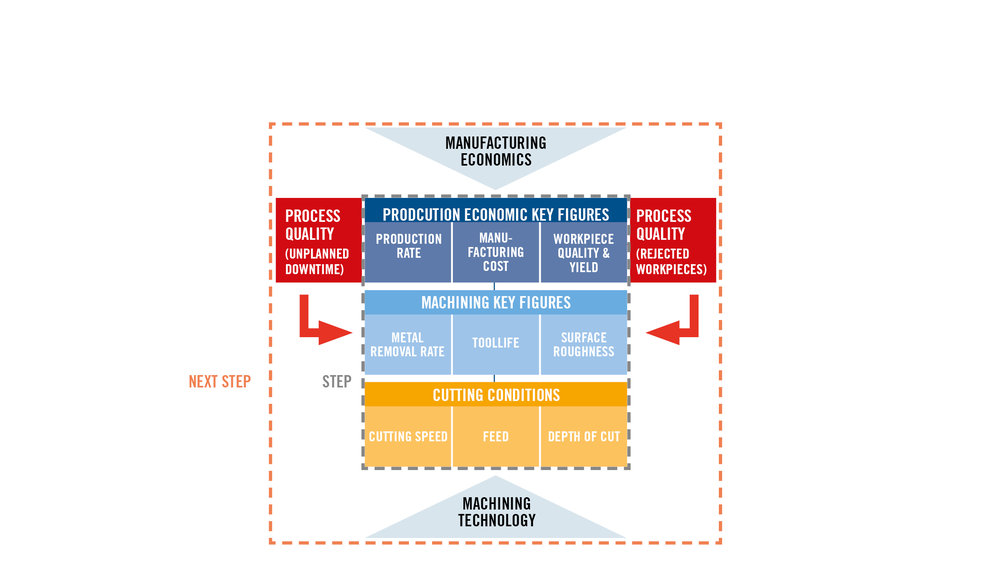
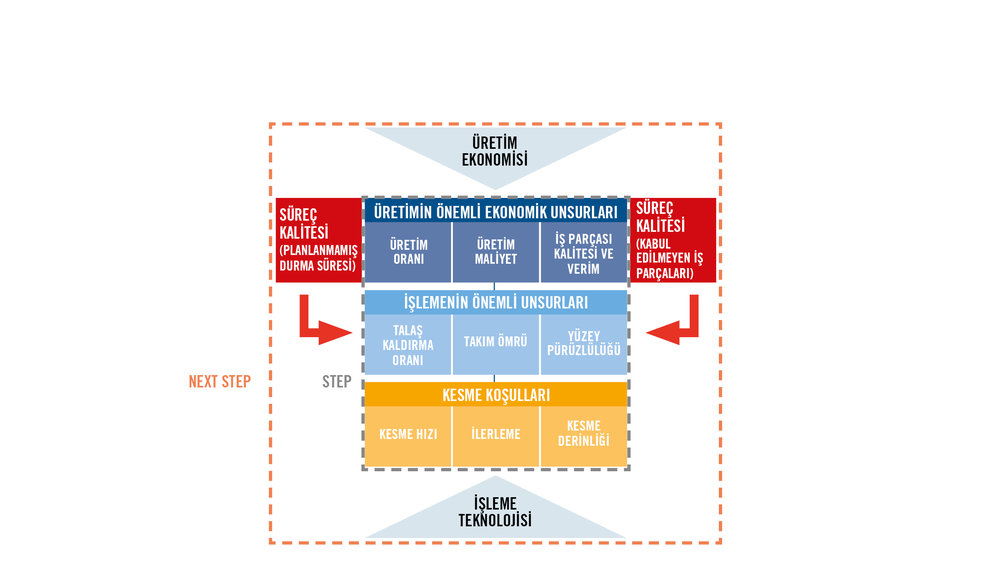
Üretim ekonomisinin temelleri
Üretim, bir dizi dönüşüm sürecinden oluşur. Bir atölye, dövme, kaynaklama veya işleme gibi bir dizi bağımsız dönüşüm işlemleriyle hammaddeden tamamlanmış veya yarı tamamlanmış iş parçaları oluşturur. Her operasyon çeşitli bağımsız unsurlardan oluşur. Örneğin, işlemenin temel unsurları kesici takım, tezgah, fikstürler ve soğutma sıvısı kullanımıdır. Bu unsurlar bir araya geldiğinde, bir üretim sistemindeki ilgili ekipmanlar ve bileşenlerden destek alan bir işleme sistemini oluşturur.
Planlama, programlama ve ekonomik yönetim fonksiyonları, bir üretim ortamını oluşturmak üzere üretim sistemini çevreler. Bir üretim ortamının ana unsuru insandır. Bugün üretimde bilgisayarlar, robotlar ve diğer gelişmiş teknolojiler yaygın bir şekilde kullanılsa da, genel olarak ortamı kontrol eden kararları insanlar alır.
İşleme süreci; takım seçimi, kesme koşulları, programlama ve iş parçası malzemesi ve fikstür ile ilgili teknik uygulama ayrıntılarına dayanır. Diğer önemli ayrıntılar, üretim hacmi gereksinimlerini ve bitmiş iş parçalarının belirli bir kalitede olmasını içerir.
Teknik uygulama ayrıntılarının ekonomik konulara bağlanmasına üretim ekonomisi adı verilir. Üretim ekonomisi biliminin amacı, ilgili tüm faktörleri dengelemektir. Teknik unsurlar iş parçası kalitesi, miktar ve zamanlama açılarından istenen sonuçları sağlarken operasyonlar, işletmenin büyümesini sağlayacak bir maliyetle gerçekleştirilmelidir.
İşlemede üretim ve maliyet dengesi üç aşamada sağlanır. İlk aşama, güvenilir bir işleme sürecinin oluşturulmasıdır. Takımların kırılması, kontrol edilemeyen talaş oluşumu ve sonuçta iş parçalarının bozulması gibi beklenmeyen olayların en aza indirilmesi önemlidir. Bir atölye, işleme sürecinde oluşturulan mekanik, termal, kimyasal ve tribolojik yükleri karşılayan veya aşan yüksek kapasiteye sahip takımlar seçerek operasyonel güvenilirlik sağlar.
Şekil 2 – STEP'te geliştirilen toplam işlenebilirlik modeli.
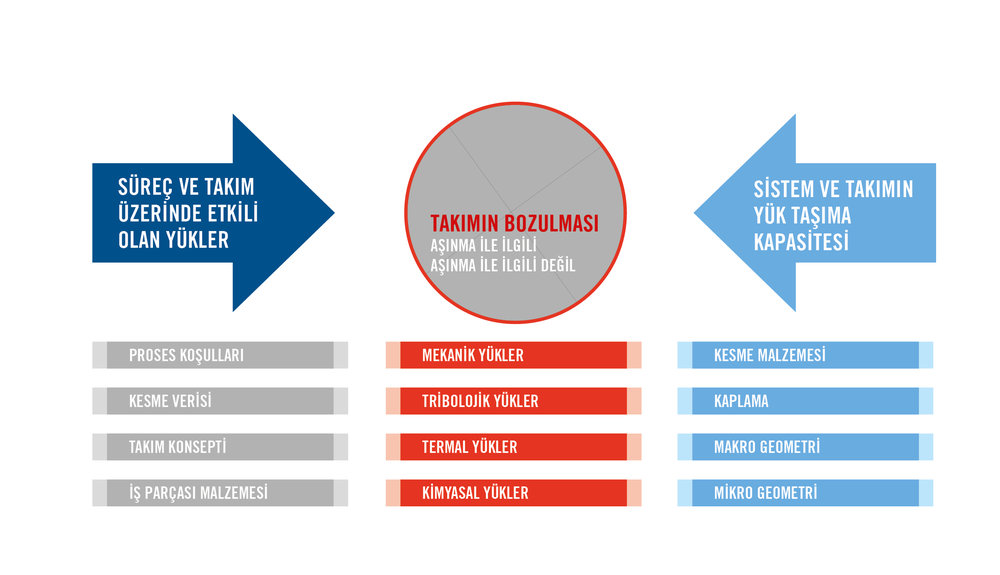
HQ_ILL_Machinability _model
Dengeli üretim ekonomisini gerçekleştirmede ikinci aşama, işleme sürecinde gerçek dünya şartlarının getirdiği kısıtlamaları yansıtan kesme koşullarının seçilmesidir. Bir kesici takımın teorik kabiliyetleri geniştir. Ancak belirli atölye gerçekleri, etkili uygulama parametreleri aralığını sınırlandırır.
Örneğin, bir takımın kabiliyetleri ve performansı, bunu uygulayan tezgahının sahip olduğu gücün miktarına; iş parçası malzemesinin işleme karakteristiklerine veya titreşime ya da bozulmaya yatkın bir parçanın yapılandırmasına göre değişir. Teoride işe yarayacak çok çeşitli kesme koşulları olmasına rağmen, ne yazık ki gerçeklerin gösterdiği kısıtlamalar sorunsuz seçeneklerin sayısını azaltacaktır.
Şekil 3'te, çok çeşitli ya da büyük hacimli kesme hızları, kesme derinlikleri ve ilerlemel ile belirli bir kesme uygulamasının çeşitli gerçekleri sonucunda uygulanan daha az çeşit ve daha küçük bir hacim gösterilmektedir.
Şekil 3 – Kesme ortamından gelen kısıtlamalar dahilinde kullanılabilecek tüm kesme koşulu kombinasyonlarını gösteren 3D örnekleme.
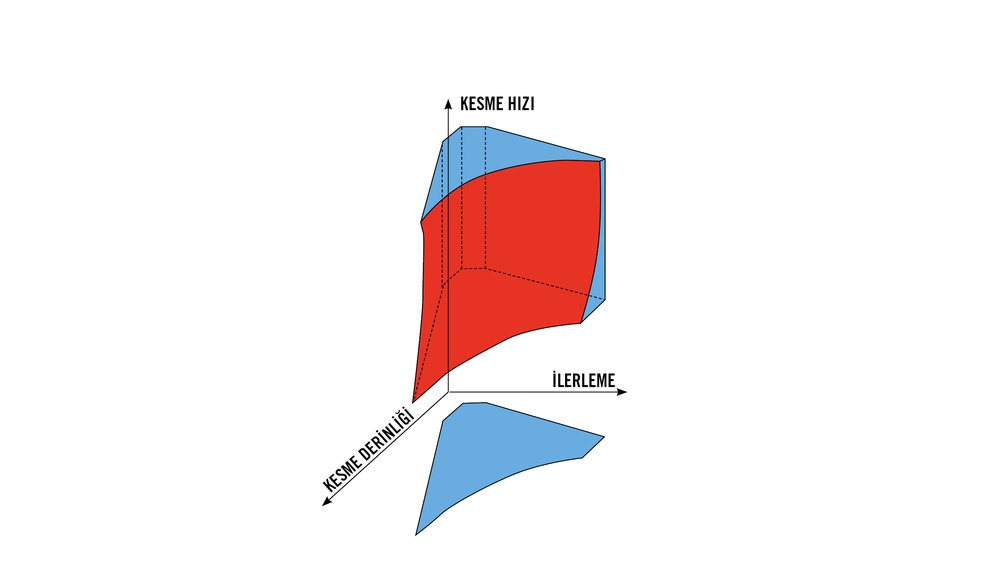
HQ_ILL_Machining_Process_cutting_conditions
Belirli bir durumun uygulama kısıtlamalarının dışında kesme koşullarının uygulanması, daha yüksek maliyetleri ve daha düşük üretkenliği de içeren olumsuz negatif sonuçlar doğuracaktır. İşleme sırasında karşılaşılan sorunların belki de yüzde 90'ı, atölye gerçeklerinin kesme işlemine getirdiği sınırlandırmalara uyulmamasından kaynaklanır.
Kesme koşulları, atölye gerçeklerine bağlı kısıtlamaları aşmadığında, operasyon teknik açıdan güvenli olur. Bununla birlikte, teknik açıdan güvenli her kesme koşulu kombinasyonu aynı ekonomik sonucu sağlamayacaktır. Değişen kesme koşulları, işleme sürecinin maliyetini değiştirir. Daha agresif ancak teknik açıdan daha güvenli kesme koşullarına geçilmesi ancak belirli bir noktadan sonra tamamlanmış iş parçalarının üretimini artırır, fakat agresif kesme parametreleri takım ömrünü kısaltacağından üretkenlik de düşecektir. Aşınan takımların değiştirilmesi için daha fazla zaman harcanacağı için ileride parçaların üretimi de azalacaktır.
Bir noktada, üretken üretim ve üretim maliyetinin dengede olduğu bir kesme koşulları kombinasyonu vardır. Şekil 4'te kesme koşulları, üretkenlik ve takım ile tezgah maliyetleri arasındaki ilişki gösterilmektedir. (Grafik yalnızca kesme koşullarıyla birlikte değişen unsurlara odaklanmaktadır; malzeme, ek yük ve yönetim ile mühendislik maliyetleri dahil edilmemiştir.) Daha agresif koşullar, eksenlerin sağında ve daha yüksek üretkenlik üstte yer almaktadır. Grafiğin ortasındaki açık mavi şerit, kesme koşullarının üretkenlik (en yüksek üretim) ve ekonomi (en düşük maliyet) ile dengeli bir kombinasyon oluşturduğu yeri gösterir.
Şekil 4 – kesme koşulları, üretkenlik ve işleme maliyetleri arasındaki ilişki. Bu şekilde basitleştirilmiş bir model gösterilmekte ve kaynakların iyi kullanılmadığı faktörler dikkate alınmamaktadır.
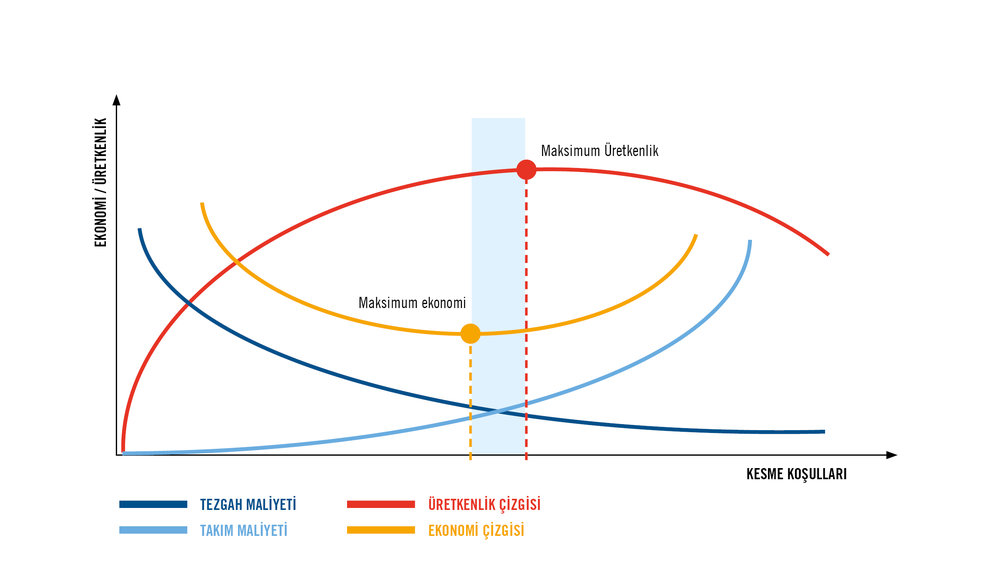
HQ_ILL_Machining_Process_relationship_cutting_conditions_productivity_machining_costs
Bu doğrultuda, dengeli üretim ekonomisini gerçekleştirmenin üçüncü aşaması, belirli bir durum için en uygun kesme koşulları kombinasyonunun belirlenmesidir. Kesme parametrelerinin istenen üretkenlik ve ekonomi düzeylerini sağladığı bir çalışma bölgesi oluşturmak için işleme operasyonundaki tüm faktörlerin dikkate alınması önem taşır.
Iskartaların üretim ekonomisine etkisi
Maalesef, dengeli üretim ekonomisiyle ilgili mükemmel bilimsel yöntemlerinin çalışması, üretim sistemindeki kaynakların iyi kullanılmasına bağlıdır. Kaynakların iyi kullanılmaması, birçok şekilde meydana gelir ve dengeyi bozar. Örneğin, 60 kW gücündeki bir tezgahın sürekli olarak yalnızca 15 kW gerektiren bir uygulamada kullanılması enerji ve gücün boşa harcanmasıdır. Bir başka durumda, bitmiş iş parçaları gerekli kalite düzeyini karşılamadığında, süreç için harcanan zaman, para ve kaynaklar, kabul edilemez bir sonuçla boşa gitmiş olur. Benzer şekilde, kalite artışı maliyeti artıracağından, istenen kalite düzeylerini gereksiz bir şekilde aşan üretim iş parçaları da kaynakların iyi kullanılmaması anlamına gelir.
Kaynakların iyi kullanılmamasıyla ilgili olarak çok açık olmayan ve daha az anlaşılan bir durum, bilgi kaynaklarının az veya yanlış kullanılmasıdır. Bir şirketteki personelin belirli bir kısmı, şirketin hedeflerine ulaşmasına yardımcı olacak bilgiye veya becerilere sahip olabilir ancak kötü iletişimden şirket içi politikalara kadar çeşitli nedenlerle, bilgi ve beceriler paylaşılmaz ve dolayısıyla, boşa harcanmış olur.
Iskartaları önlemeye yönelik araçlar
Kaynakların iyi kullanılmaması tanımlanıp kategorilere ayrıldıktan sonra, atölyenin bunu azaltacak veya ortadan kaldıracak bir plan oluşturması gerekir. Burada, bir üreticinin kaynakların iyi kullanılmadığı uygulamaları tespit etmesini, ölçmesini ve en aza indirmesini sağlayacak çok çeşitli araçlar mevcuttur. Örneğin, takım kullanımı, yönetim ve bozulma analizi sorunlu alanları gösterir.
Bu tür analizlerde, personelin aşınmış olarak tanımladığı takımların yüzde 20 ila 30 kadarının aslında hala kullanılabilir durumda olduğu yani kalan takım ömrünün boşa harcandığı görülmüştür. Net takım aşınması kriterleri belirlemek ve standartların atölye personeline anlatılması, boşa harcanan takım ömrünü önemli ölçüde azaltacaktır.
Benzer şekilde, tezgah durma süresi analizleri, kurulum, programlama ve takım değiştirme gibi faaliyetlerde harcanan süreyi ölçer. Bu analizler genellikle daha iyi bir anlayış, yürütme ve gerekli ancak zaman alan faaliyetlerin koordine edilmesiyle tezgah durma sürelerinin yüzde 50 ila 60 oranında önlenebileceğini göstermektedir.
Bilgi kaynaklarının boşa harcanmasına yol açan personel sorunlarının giderilmesine çalışılırken düzenlenen görüşmeler, anketler ve eğitim programları aracılığıyla, farkına varılmayan bilgi ve becerilerin yanı sıra birçok yararlı bilgi de ortaya çıkabilir. Sonuç olarak, çalışanlar işlerini daha iyi yapar ve personel üretkenliğini en üst düzeye çıkaracak kabiliyetler edinir.
Değer katan, değer sağlayan ve gereksiz faaliyetlerin yönetimi
20. yüzyılın başlarında, Amerikalı endüstri mühendisi Fredrick Taylor, atölye operasyonları üzerinde çalışmalar yaptı ve bir süreçte, son ürüne değer katmayan faaliyetlerin ortadan kaldırılmasıyla üretkenlik iyileşmesinin sağlanabileceğini önerdi. Modern "ince" üretim kılavuzları, bu düşünce yolunu izlemektedir.
İşleme operasyonlarında, gerçek değer katan tek faaliyet takımın metali gerçekten kesmesi ve talaş üretmesidir. Değer sağlayan faaliyetler olarak belirtilen parça yükleme ve takma gibi diğer eylemler, üretilen ürüne doğrudan değer katmaz ancak değer katan faaliyetin gerçekleşmesi için gereklidir.
İşleme sistemindeki üçüncü bir faaliyet grubu da gereksiz faaliyetlerdir. Bu faaliyetler ne değer oluşturur ne de değer oluşturulmasını sağlar; bunun yerine, hiçbir fayda sağlamadan kaynakları tüketir. Bunlar sadece kaynakların boşa harcandığı durumlardır. Sorun çözme, gereksiz faaliyetlere bir örnektir. Bir süreç en başta doğru tasarlanır ve kontrol edilirse herhangi bir sorun ortaya çıkmaz ve bunun çözümü için zaman harcanmaz.
Şekil 5 – Bir işleme atölyesinin ve bununla ilişkili tüm unsurların şematik resmi.
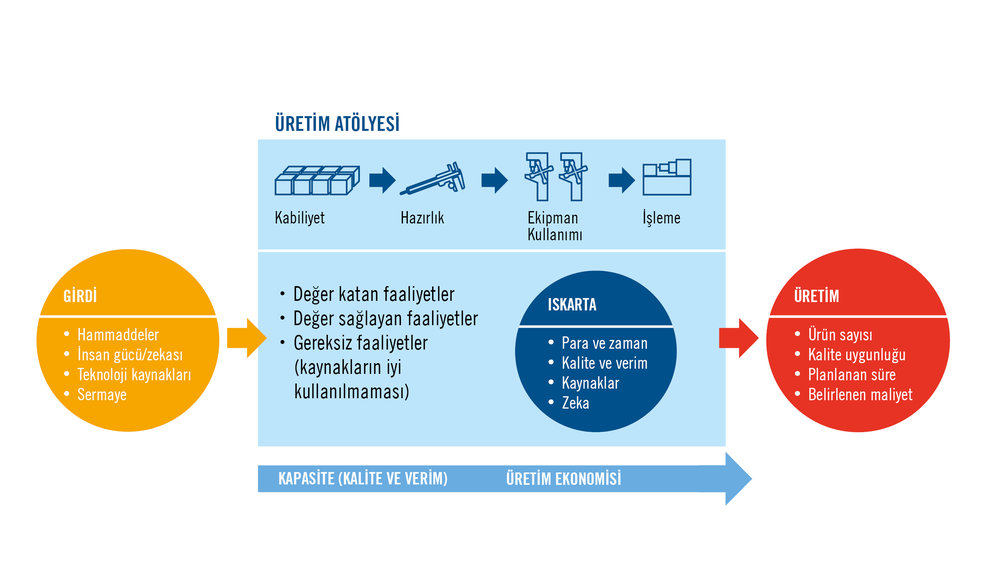
HQ_ILL_Machining_process_workshop
Sonuç
Geçmişte uzun bir süre, gereksiz faaliyetler üretim sürecinin bir parçası olarak kabul edilmiş ve dengeli üretim ekonomisinin gerçekleştirilmesinde önemli bir aksamaya neden oldukları düşünülmemişti. Şu anda, dikkatler gereksiz faaliyetlerin ortadan kaldırılmasına veya en aza indirilmesine yönelmiştir. Üretkenlik veya kapasite planlamasının odağında, gereksiz faaliyetlerin ortadan kaldırılması, değer sağlayan faaliyetlerin en aza indirilmesi ve değer katan faaliyetlerin optimize edilmesi bulunmaktadır. (Bkz. Şekil 6)
Şekil 6 – Değer katan faaliyetler (turuncu), değer sağlayan faaliyetler (mavi) ve kaynakların boşa harcandığı faaliyetlere (kırmızı) genel bakış. En iyi üretim performansının en iyi şekilde gerçekleştirilmesinde ana faktör insan faktörüdür (gri).

HQ_ILL_Machining_system_process
Kaynakların iyi kullanılmaması durumu ortadan kaldırıldığında, teorik üretim ekonomisi pratik üretim ekonomisine dönüşür. Bu noktada, üretim ekonomisindeki ilerleme doğrudan şirket başarısına uygulanabilir. Bununla birlikte, kaynakların iyi kullanılmadığı her durumu ortadan kaldırma çabasında dikkatli olunmalıdır. Kaynakların daha iyi kullanılmasını sağlayacak faaliyetlerde yatırım geri dönüşünün ölçülmesi önemlidir. Kaynakların iyi kullanılmadığı belirli bir olayın tamamen ortadan kaldırılması, ekonomik açıdan kaynakların iyi kullanılmamasını tamamen veya kısmen kabul etmenin ve bu şekilde devam etmenin daha iyi olabileceği çok büyük bir yatırımı gerektirebilir. Bu tür kararlar, uygun sayısal analizlerin ve şirket hedefleri ile felsefesini nasıl etkileyeceğine yönelik şirket içi tartışmaların ardından verilir.
Yan çubuk:
Seco Danışmanlık Hizmetleri
Ürün üretmek giderek daha karmaşık hale geldiğinden, kullanıcılar yeni teknolojilerden en fazla faydayı sağlamak için giderek artan miktarda uygulama yardımına ihtiyaç duymaktadır. İşlemede, birinci yardım düzeyi, belirli bir operasyon için doğru takımın seçiminde yol gösterici bilgiler sağlanmasıdır. Bir takım seçildikten sonra, ek bilgiler en uygun kesme koşullarının seçimini, soğutma sıvısı kullanımını ve diğer konuları kolaylaştırır. Ardından, bir takım söz konusu operasyonda beklendiği gibi çalışmazsa takım tedarikçisi, sorun giderme yardımı sağlayabilir. Bu üç yardım modu, geleneksel işleme hizmetlerini oluşturur.
Bir iş parçasının bir veya daha fazla tezgahta birden çok operasyon sonucu üretildiği durumlarda işleme hizmeti tek bir uygulamadan bir süreci kapsayacak şekilde genişler. Bu durumda, son kullanıcılar verimliliği ve üretkenliği en üst düzeye çıkarmak için operasyon sırasının ayarlanması, iş parçası yönetimi ve diğer faktörler konusunda yol gösterici bilgilere gereksinim duyar. Bu yardım düzeyi, mühendislik hizmetleri olarak adlandırılabilir.
Giderek daha sık bir şekilde, üreticiler bir atölye veya kuruluşun tamamında fonksiyonların, üretimin ve maliyet kontrolünün iyileştirilmesi arayışına girmektedir. Bu durumlarda, bazı bağımsız danışmanlık şirketleri, yönetim veya üretim danışmanlığı olarak tanımladıkları görevi gerçekleştirir. Bununla birlikte, bir üretim kuruluşunu doğru bir şekilde değerlendirmek için işletmenin temel operasyonlarının tam olarak anlaşılması gerekir.
İşleme süreçleri ve işlemeyle ilgili uzun ve kapsamlı anlayışını uygulayan Seco, onlarca yıldır geleneksel işleme hizmetleri, mühendislik hizmetleri ve bir ölçüde danışmanlık hizmeti de sunmaktadır. Bu hizmetler, şarta bağlı veya duruma özel olarak sunulmaktaydı ancak 2016'da Seco, müşterilerine daha geliştirilmiş ve uyumlu bir üretim hizmetleri dizisi sağlamak için Danışmanlık Hizmetlerini oluşturdu.
Seco Danışmanlık Hizmetleri, çok çeşitli kaynaklar ve teslim yöntemleri sağlamaktadır. Takım seçimi ve uygulama yardımı, işleme tesisindeki acil üretkenlik ihtiyaçlarını karşılamak için günün her saati çevrimiçi olarak sunulmaktadır.
Mühendislik hizmetleri elektronik iletişimle başlayıp gerekirse müşteri yerinde ziyaretleri de kapsayabilir. Seco Danışmanlık Hizmetleri, bir atölyedeki her fonksiyonun çalışmasını içeren kapsamlı analizler ve kılavuz bilgileri de sağlayabilir. Bu hizmetler, tezgah bakımı, atölye düzeni, lojistik ve kurumsal fonksiyonlarla ilgili danışmanlığı içerebilir. Personelin beceri ve bilgi sorunlarıyla ilgili tavsiyeler ve kuruluşun üretim stratejilerinde uygulanan üretim teknikleriyle ilişki ve maliyetle ilgili konular da buna dahil edilebilir.
Her Seco Danışmanlık ilişkisi, NEXT STEP konseptine dayanır ancak, aynı zamanda katılımcı kuruluşun özel gereksinimlerine de uyarlanmaktadır ve Seco ile müşteri arasında, ortak hedefe ulaşmayı amaçlayan bir diyalog olarak sağlanır.